Table of Content
Ask what the sub is like on the job, if they stay on schedule, and if they do good work. Hiring good people is usually worth the little bit of extra money it may cost. You’ll be able to trust them and won’t need to be on-site to constantly supervise. Popular Mechanics has a great read on the different types of decking material if you require more information. Redwood – easy to work with, it naturally resists decay and insects, and warp resistant. It also is a low maintenance wood that can be left to weather on its own.
Therefore, as part of your preparation, you should install your HVAC system , along with gas, waste, plumbing, and electrical lines. Local legal requirements – every locality has its own set of laws and regulations regarding construction practices. When completing a modular home the finish work is typically confined to drywall, light trim, and floor finishing/seeming work.
Great Shipping Container Homes Available in Florida
Impresa Modular will coordinate closely with you to insure success at this critical step. Once the bank loan is approved, surveyors can stake out the corners of the house. This is the first important step in construction because everything else is based on those survey stakes. They are especially important when you have got setbacks and easements to worry about. Pressure Treated – there are many types of pressure treated but the most common is made from pine.
Copyright © 2022 Express Ramps - The Wheelchair Ramp Experts. Easily Portable & Handrails can be installed on either side. It’s important to have a detailed plan before you start construction. This isn’t just the house plan, but a construction schedule and work details that are as specific as possible. It’s important to know that you are in charge of making sure that the driver has appropriate access to the site.
Impresa Modular
However, they’ll handle this process if you’ve opted to receive a full-service package from your manufacturer. Technically speaking, modular homes are houses that come to you pre-assembled. Flat-packed, panelized, or any other type of building that comes while separated into components is usually called prefab.
We’ve used the word “assemble” here, but this step also pertains to the setup process of fully-built structures. Your home will be built primarily using automated, precise machinery, optimizing the structure’s overall quality and durability. Moreover, the process is carried out in a climate-controlled space, meaning all components are handled in their ideal environment. When choosing a layout, consider that the more you customize and adjust your future home’s components and features, the costlier it will become. Therefore, when drawing your foundation, floor, and general site plans, be careful not to be over-ambitious if on a tight budget. You’ll need to decide how you want your modular home delivered.
Go Green with a Metal Roof: A Step-By-Step Guide
Faucets and exposed pipes left unprotected Friday night will surely result in a problem. Eastern Shore Ace Hardware had customers coming in all week concerned about the arctic freeze. With the ready-made products sold out, employees have been offering other advice. I knew it was going to be freezing about daylight, so I went ahead and checked the water…went ahead and start dripping some. One of them was actually a frozen brass spigot so I had a torch, went ahead and lit it and got the water flowing back again,” Williams said.
However, they are still as great as a temporary option. Mobile home steps can be made of several different materials. Depending on your budget and preference, you can choose the best fit for you. The first step on our list is this set, made of treated plywood and lumber. It is designed to combat decay, rotting as well as warping.
Once received, you’ll also need approval from your local code enforcement agency before proceeding with the preparation process. On set day you will be responsible to insure that the crane has the ability to move to its required position to setup and access each of the modular home sections. This is important to reduce the overall time it takes to get your home onto the foundation and under roof. A two section home is set and weathered in within one day. A home with 6-8 sections can usually be completed in 2-3 days.
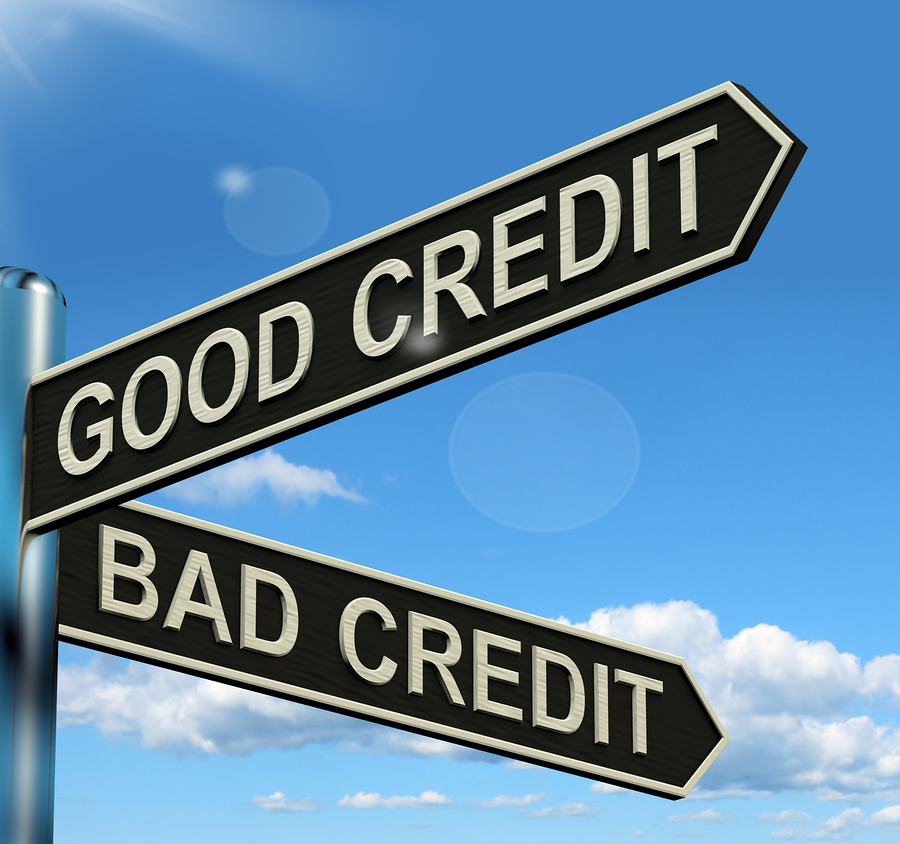
If you have chosen specialty siding, the amount of work to be completed onsite vs. at the factory will vary. The excavators dig the hole for the foundation, and your chosen type of foundation is installed. There are a few key items to think about when buying a site for new homes construction. For proper drainage, the house shouldn’t be in a low spot or at the bottom of a hill where runoff will head.
However, plan exactly where it will go on your building site. It can’t interfere with construction vehicles, crane locations, or the staging/storage area for your modular home sections. As always, Impresa Modular is ready to assist you with any questions you may have. The whole process may only take a week and the steps aren’t that complex, but it’s critical to be very sure that each is done correctly. A modular home is built perfectly square at the manufacturing facility.
But this is where the real legwork begins so the whole building process will go smoothly. First, you’ll need to be pre-approved for a standard “end” mortgage before talking about a construction loan. Once that’s done, the construction loan process can begin. Selecting a lender is the first and most important order of business.
No comments:
Post a Comment